Condition Monitoring
Condition Monitoring Solutions With XMPro
In today’s dynamic industrial environment, Condition Monitoring is not just an option—it’s a critical necessity. XMPro stands as a leader in this field, harnessing its Intelligent Business Operations Suite, advanced AI capabilities, and real-time data integration to revolutionize how businesses monitor, maintain, and optimize their assets.
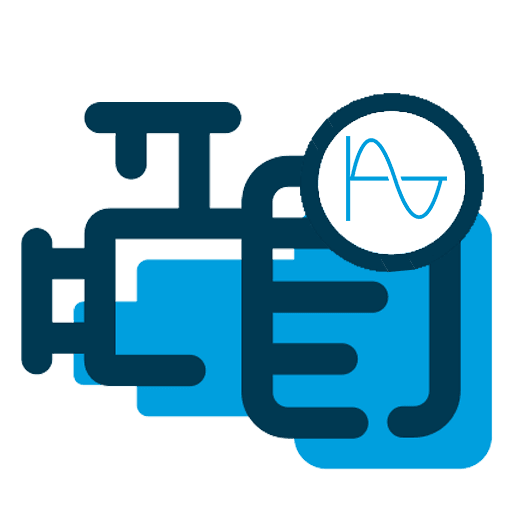
XMPro’s Model-Based Condition Monitoring Approach
Combine the best of Physics with the best of AI for the best condition monitoring from an Intelligent Digital Twin
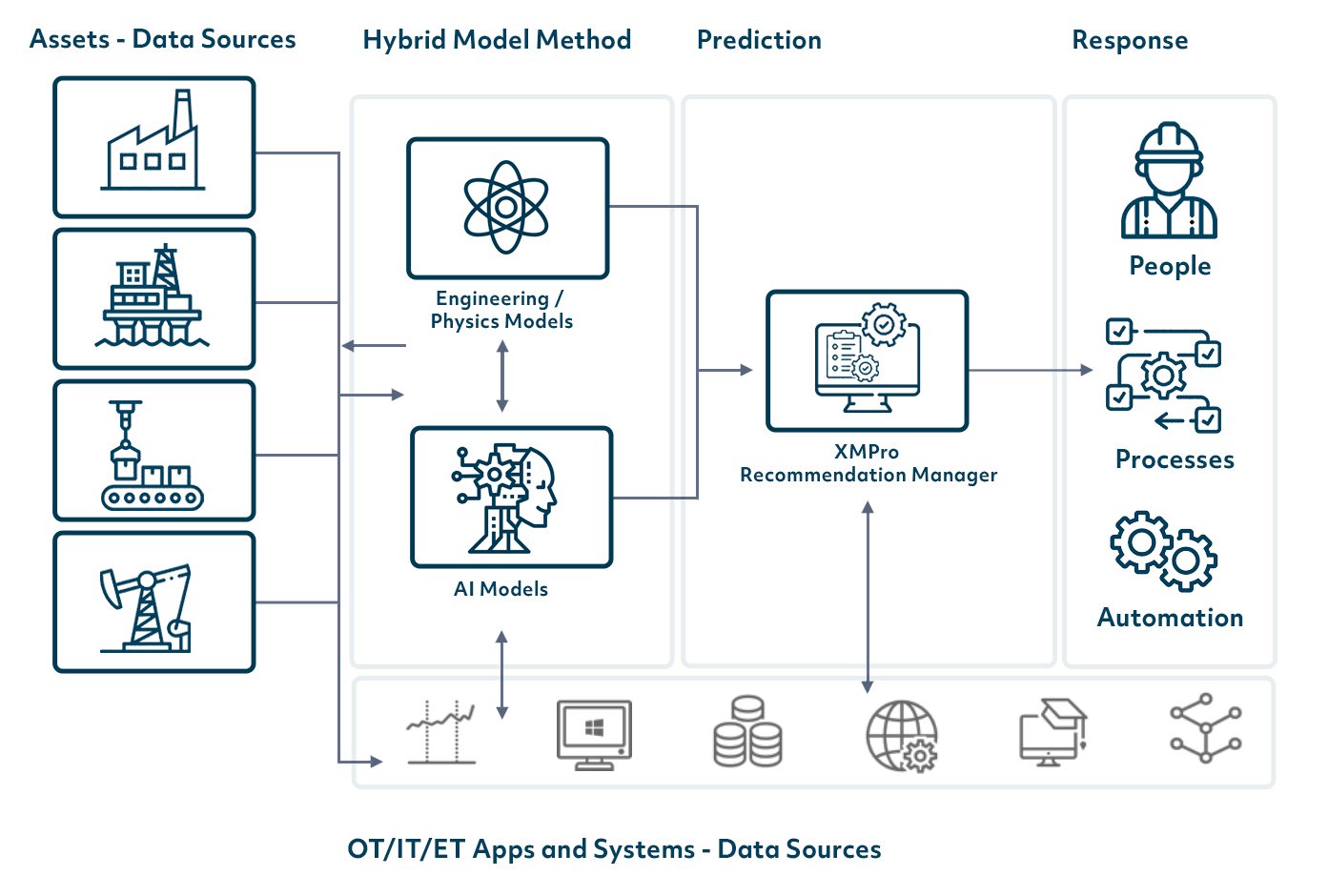
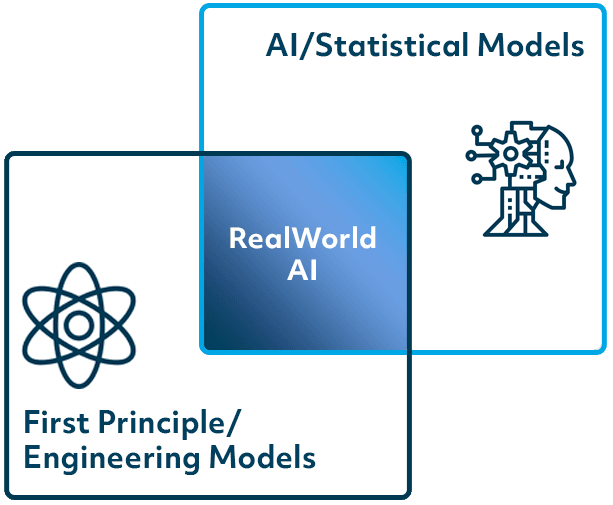
Use XMPro Blueprints for Quick Time To Value
Easily import Blueprints, Accelerators and Patterns into your environment, providing a starting point for configuring your own solutions.
Getting Started: XMPro’s 3-Step Process To Success:
Our Unique 3 Step Process to Prioritize, Predict, and Propel at Scale
XMPro’s 3-step process in model-based condition monitoring uniquely combines continuous ‘bad actor’ analysis, a hybrid of traditional and AI models for real-time monitoring, and provides ready-to-use blueprints for quick implementation. This structured and tech-enhanced approach, along with accelerated deployment, sets it apart in the predictive maintenance market.
Step 1. Prioritize Bad Actors First
Start your condition monitoring journey by focusing on the most critical elements. XMPro’s Intelligent Digital Twins continually monitor operational assets, providing constant analysis. By identifying and focusing on these critical components, our solution generates practical recommendations, ensuring your condition monitoring efforts are precisely targeted for optimal outcomes.
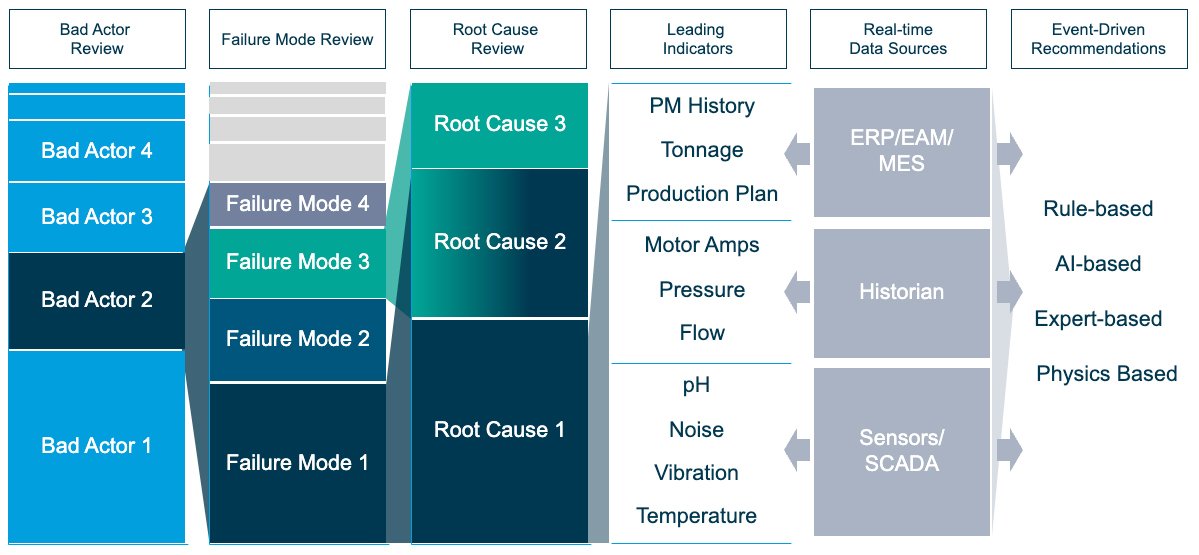
Step2. Monitor in real-time with a hybrid model-based approach
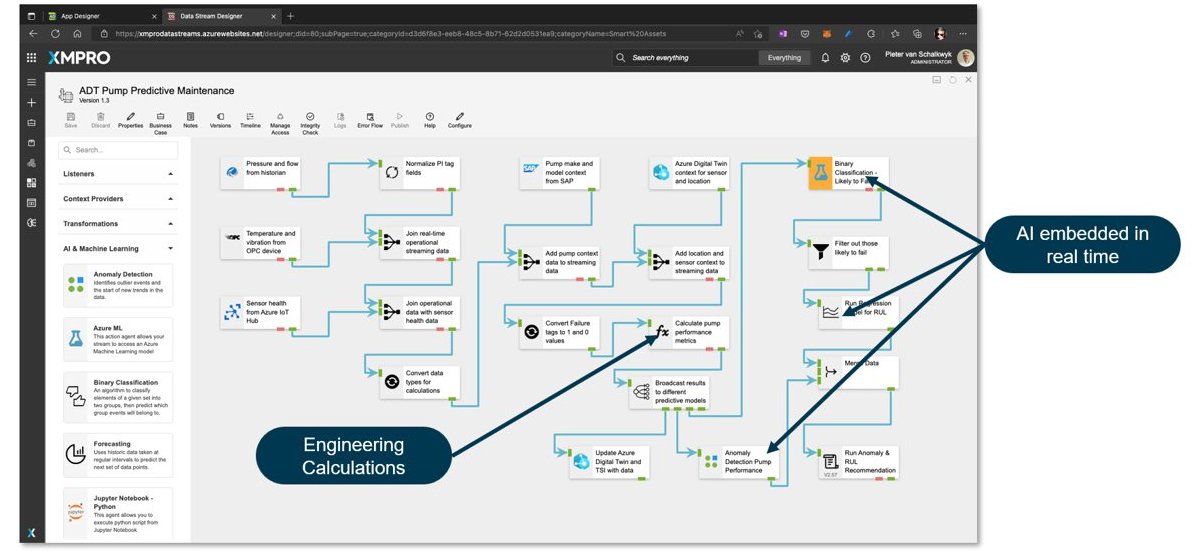
Experience the power of the XMPro hybrid model-based approach, seamlessly integrating traditional engineering principles with agile AI models. Our approach delivers real-time insights and facilitates proactive measures, safeguarding against potential failures and quality discrepancies.
Step 3. Quick Time to Value with Blueprints and templates
Expedite your condition monitoring implementation with our ready-to-use blueprints and templates. XMPro offers a comprehensive array of starting blueprints for various asset classes, ensuring a smooth and effective onset to your condition monitoring endeavors.
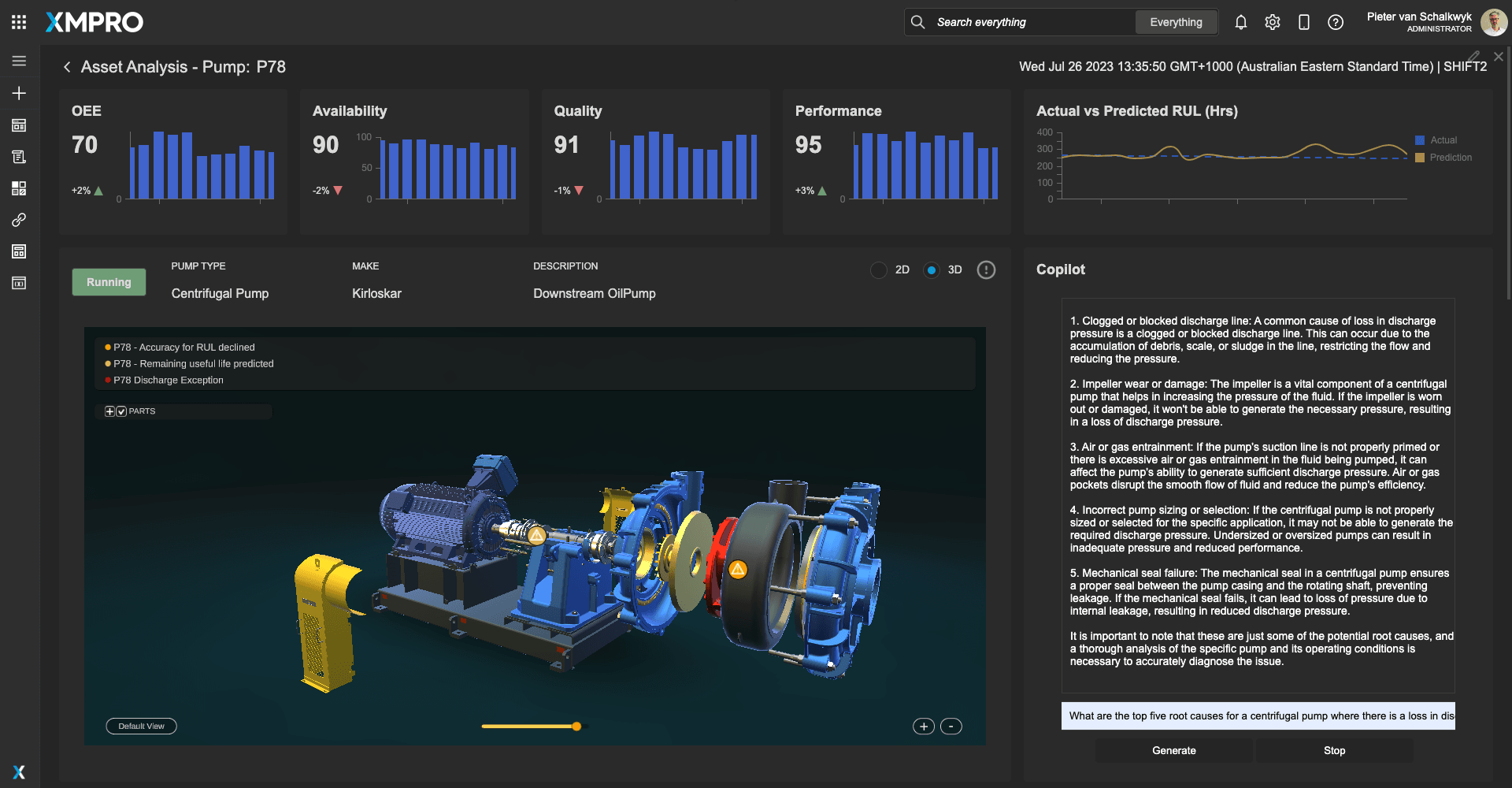
XMPro, Your All-In-One Condition Monitoring Solution:
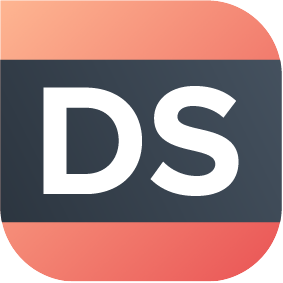
Wield Your Data Powerfully In Real-time with XMPro Data Stream Designer:
- Integrate data from all of your IoT devices, operational systems, and a myriad of external sources using our extensive integration library.
- Sanitize, wrangle and extract meaning from your data using our powerful action agent library.
- Perform advanced data transformation in real-time.
- Embed AI-models and machine learning capability within real-time dataflow.
- Easily design and visualise your data flow from origin to action using intuitive drag and drop functionality.
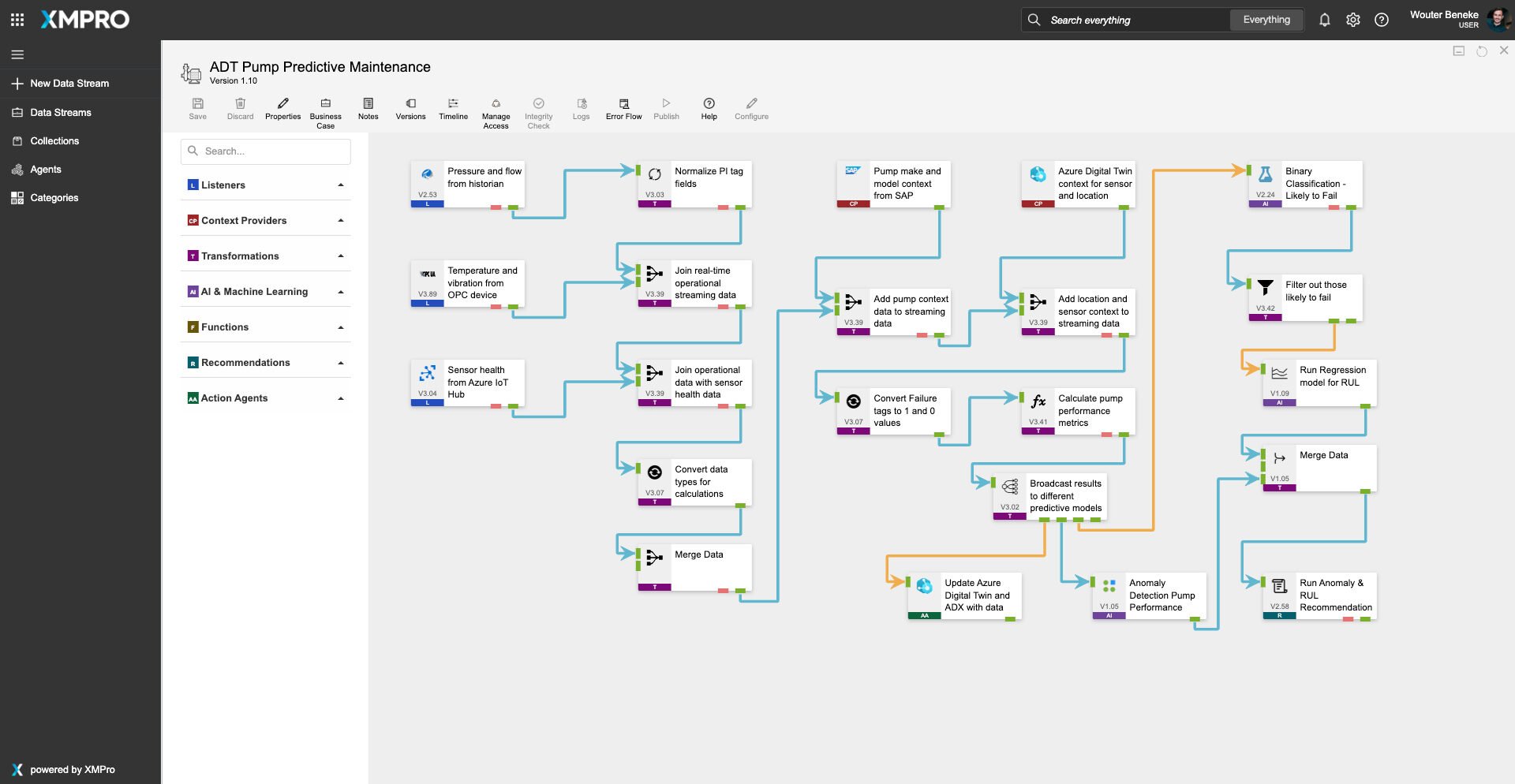
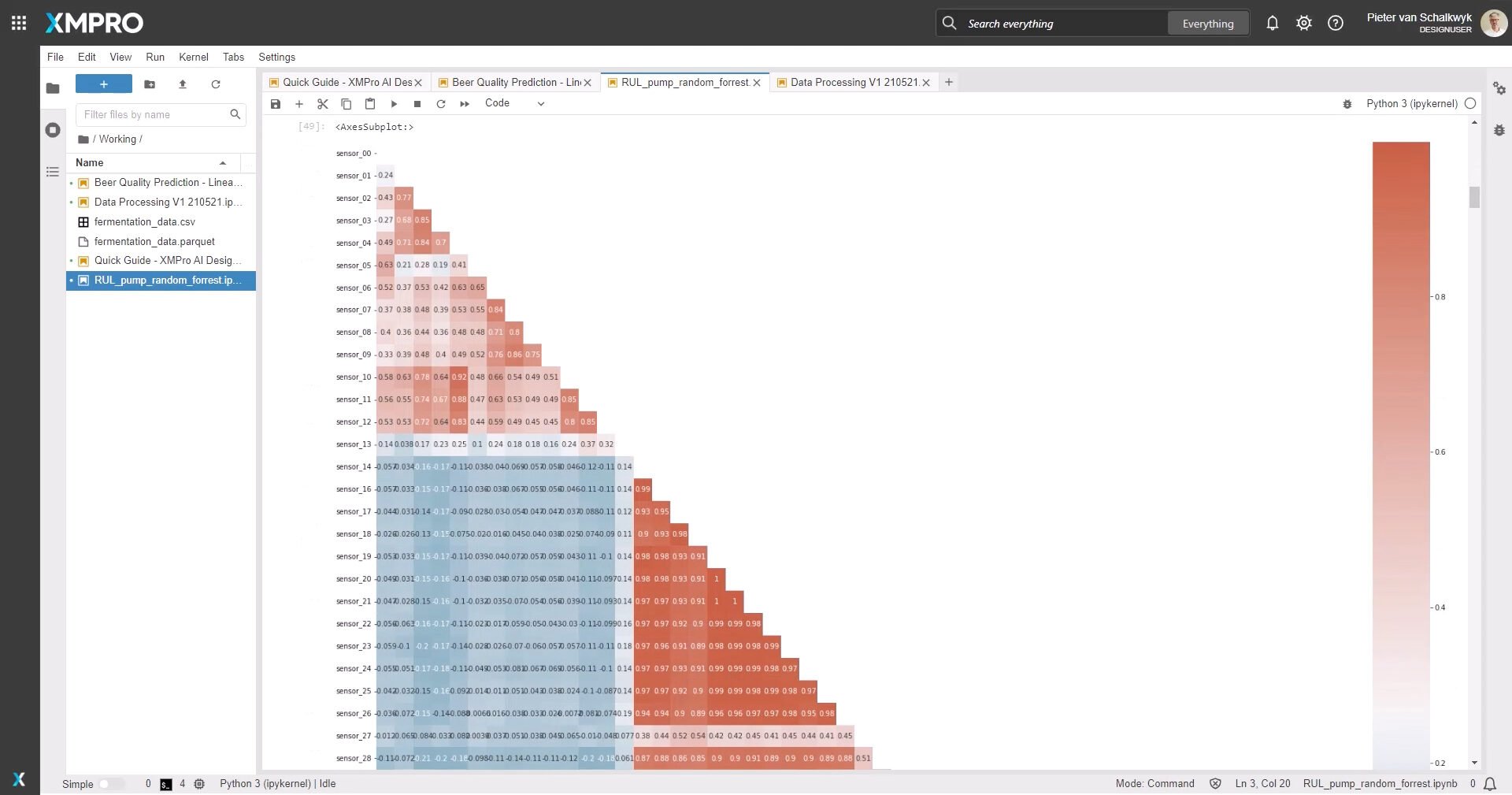

AI-driven Insights with XMPro AI:
- Seamlessly integrate AI models that not only help to prevent equipment failure, but self-learn for continuous improvement.
- Transform AI Models into powerful assets that drive business growth and efficiency through goal-seeking behaviour.
- Leverage XMPro’s AI capabilities to enhance decision support and automation using large language models securely trained on your business data.

Comprehensive Visualizations with App Designer:
- Interactive dashboards provide a holistic view of operations.
- Customize your app designs with a user-friendly drag & drop system.
- Share visual reports with stakeholders for informed decision-making.

Prescriptive Recommendations:
- Receive actionable insights based on a combination of business rules and AI logic.
- Ensure users receive the most appropriate next steps when a specific event occurs.
- Monitor actions against their outcomes for continuous improvement.
What Happens When You Get This Right?
CLIENT CHALLENGE:
In order to maximize underground mining operations, the underground conveyor system, a frequent cause of unplanned downtime, needed to reduce its downtime by 30% as an initial target for a predictive maintenance solution

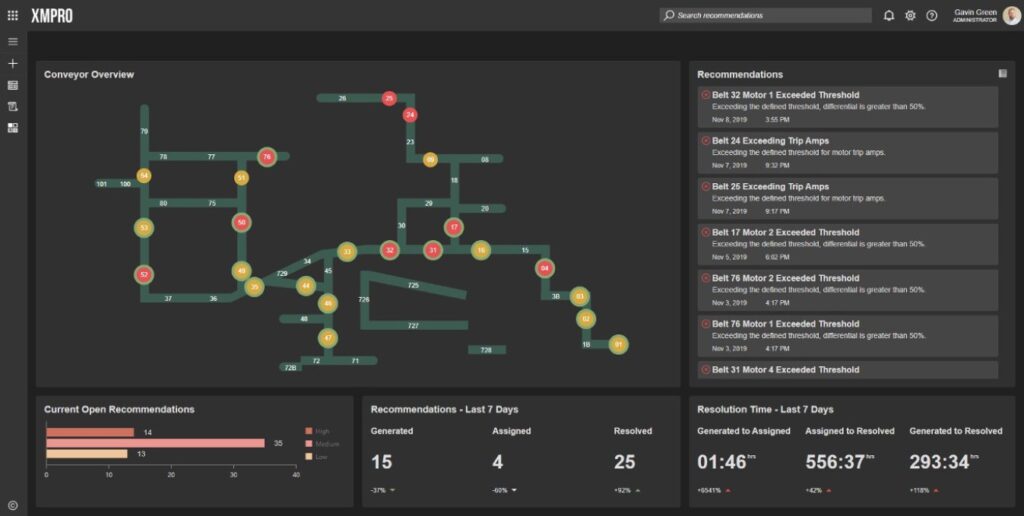
XMPRo SOLUTION
XMPro actively monitors 52 conveyors (spanning over 80+km) in real time, predicting fluid coupling and lagging failures with prescriptive recommendations.
Benefits:
Within five months, the solution identified a potential saving of 184 hours of borer downtime, equating to 44k product tonnes. Exceeding the target, the solution achieved over a 80% reduction in downtime for fluid coupling failures. It now monitors multiple asset types across several mines
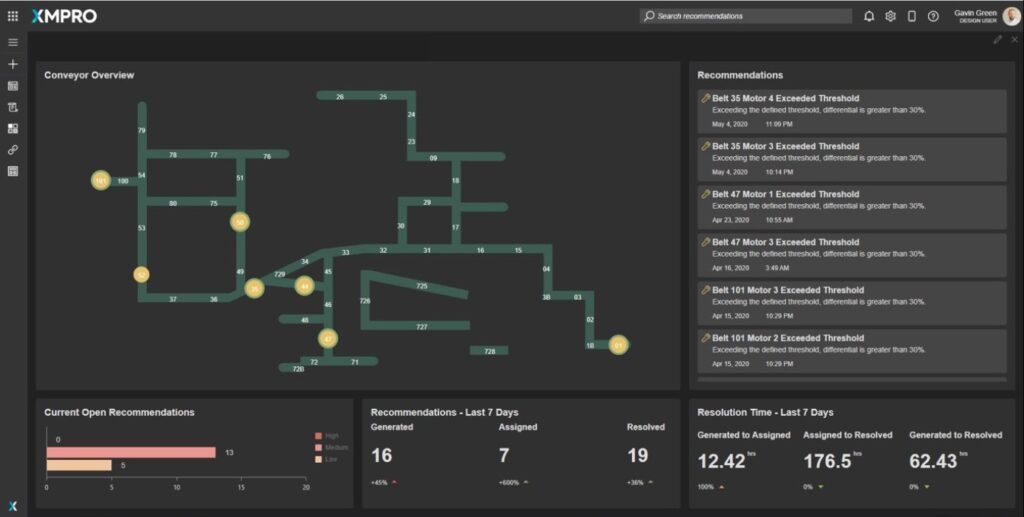
Not Sure How To Get Started?
No matter where you are on your Condition Monitoring journey, the expert team at XMPro can help guide you every step of the way – We have helped clients successfully implement and deploy in only a matter of weeks!
Request a free online consultation for your business problem.
"*" indicates required fields