Process Optimization In The Beer Processing Industy
XMPro Solution For Process Optimization in The Beer Processing Industry.
Introduction
The beer processing industry is characterized by its intricate blend of art and science, with each step in the brewing process contributing to the final product’s flavor, clarity, and quality. Process optimization in beer processing is crucial for breweries aiming to enhance efficiency, maintain product consistency, and meet the ever-evolving tastes of consumers. This use case explores the application of XMPro’s Intelligent Digital Twin Suite (iDTS) to streamline brewing operations, from raw material selection to fermentation and packaging, ensuring each batch of beer meets the highest standards of quality and taste.
The Challenge
Crafting beer that consistently meets consumer expectations while remaining cost-effective and sustainable presents a series of challenges. Breweries must navigate the complexities of raw material variability, fermentation control, energy consumption, and quality assurance, all while adhering to strict regulatory standards.
Raw Material Variability: Managing the quality and consistency of raw materials such as hops, malt, and water.
Fermentation Control: Optimizing fermentation conditions to ensure consistent flavor profiles and alcohol content.
Energy and Water Efficiency: Reducing the consumption of energy and water throughout the brewing process to enhance sustainability.
Quality Assurance: Ensuring each batch meets strict standards for taste, clarity, and purity.
Scalability and Flexibility: Adapting production processes to accommodate seasonal brews and new product lines without compromising quality.
The Solution: XMPro’s Intelligent Beer Process Optimization Solution for the Beer Industry..
XMPro’s Intelligent Digital Twin Suite (iDTS) offers a comprehensive solution designed to address the multifaceted challenges of beer processing. By leveraging real-time data, predictive analytics, and automated process adjustments, XMPro iDTS enables breweries to achieve unparalleled efficiency, consistency, and quality in their brewing operations.
Key Features
Real-time Monitoring of Brewing Conditions: XMPro iDTS’s continuous monitoring of critical brewing parameters such as temperature, pH, and fermentation activity allows for immediate adjustments, ensuring optimal conditions are maintained. This capability not only guarantees the consistency of flavor profiles and alcohol content across batches but also significantly enhances the overall quality of the beer, meeting consumer expectations for taste and purity.
Predictive Analytics for Raw Material Utilization: By forecasting the impact of different raw material batches on beer quality, XMPro iDTS enables breweries to make precise adjustments to their recipes. This predictive approach maximizes beer quality and consistency, effectively managing the variability in hops, malt, and water, and ensuring that each batch of beer lives up to the brewery’s standards.
Automated Efficiency Optimization: XMPro iDTS automates the optimization of energy and water usage throughout the brewing and cleaning processes, significantly reducing operational costs and bolstering sustainability efforts. This not only supports breweries in their green initiatives but also ensures that production is as cost-effective as possible, without compromising on the quality of the beer produced.
Quality Control and Traceability: The suite provides comprehensive monitoring and documentation for each brewing batch, enhancing traceability and quality assurance. This level of control ensures that breweries can easily comply with regulatory standards and build consumer trust by consistently delivering high-quality beer.
Scalable Production Processes: XMPro iDTS facilitates flexible and efficient scaling of production processes to accommodate different beer types and seasonal variations. This flexibility allows breweries to quickly respond to market demands and trends without sacrificing the quality or consistency of their products, enabling them to stay competitive and innovative in the rapidly evolving beer industry.
Discover XMPro’s Process Optimization Solution for the Beer Processing Industry.
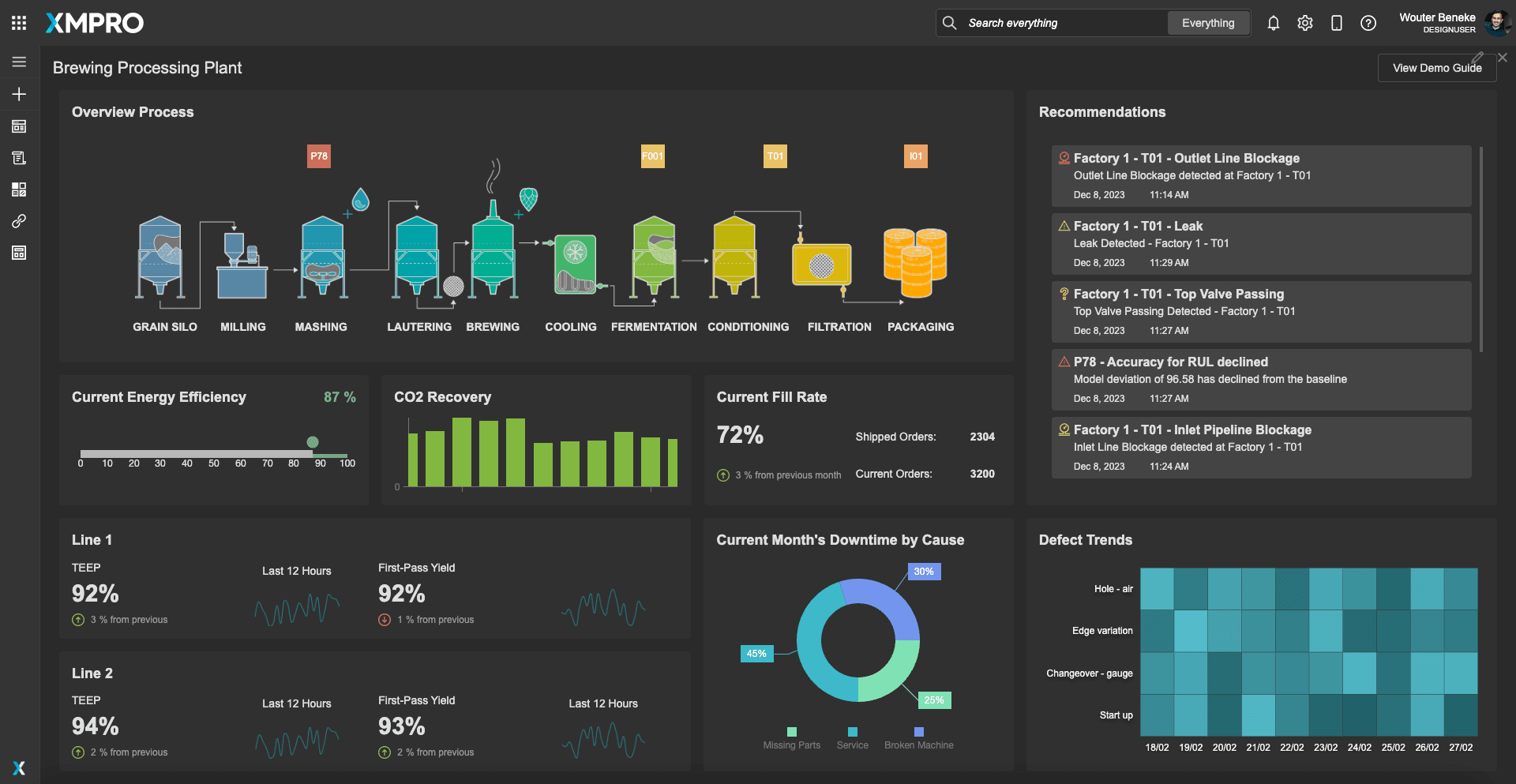
Figure 1. Real-Time Beer Processing Plant Overview Dashboard
Overview
This cutting-edge dashboard is designed for professionals in the beer industry tasked with overseeing operations across multiple brewing facilities. It offers a detailed view of the entire beer production process, from grain selection to packaging, across various locations. The dashboard’s interactive layout dynamically updates to show the operational status of each stage in the brewing process, providing a comprehensive overview of efficiency, system health, and compliance with quality standards.
Key Features
Integrated Brewing Process Monitoring: Showcases real-time data on key brewing stages such as mashing, lautering, fermentation, and conditioning across all facilities. Operational states are visually represented with color-coded indicators to highlight performance levels and alert conditions, ensuring a seamless brewing operation.
Performance Optimization Alerts: Employs sensor data and analytics to pinpoint optimization opportunities within the brewing process. It identifies areas needing immediate attention, such as adjustments in fermentation temperature or malt quality issues, to maintain product quality and process efficiency.
XMPro Co-Pilot Integration: Features integration with XMPro Co-Pilot, utilizing AI and machine learning models trained on proprietary brewery data. This provides actionable intelligence and process automation, enhancing the brewing operation’s responsiveness and adaptability.
Facility-Specific Analysis: Delivers in-depth insights into individual breweries, including performance metrics, recent maintenance activities, and predictive maintenance forecasts. This enables targeted operational strategies to optimize each facility’s brewing process.
Actionable Alerts and Strategic Recommendations: Generates precise recommendations for operational improvements and maintenance interventions. These are tailored to address the specific challenges of beer production, such as optimizing CO2 recovery rates and reducing downtime causes.
Comprehensive Status Overview: Offers a summary view of the health and performance of brewing assets, providing managers with a quick assessment tool to oversee strategic operations across the organization effectively.
Enhanced Navigation and Accessibility: An intuitive user interface and search functionality allow for easy access to detailed data on brewing processes, improving the efficiency of operational management across multiple brewing sites.
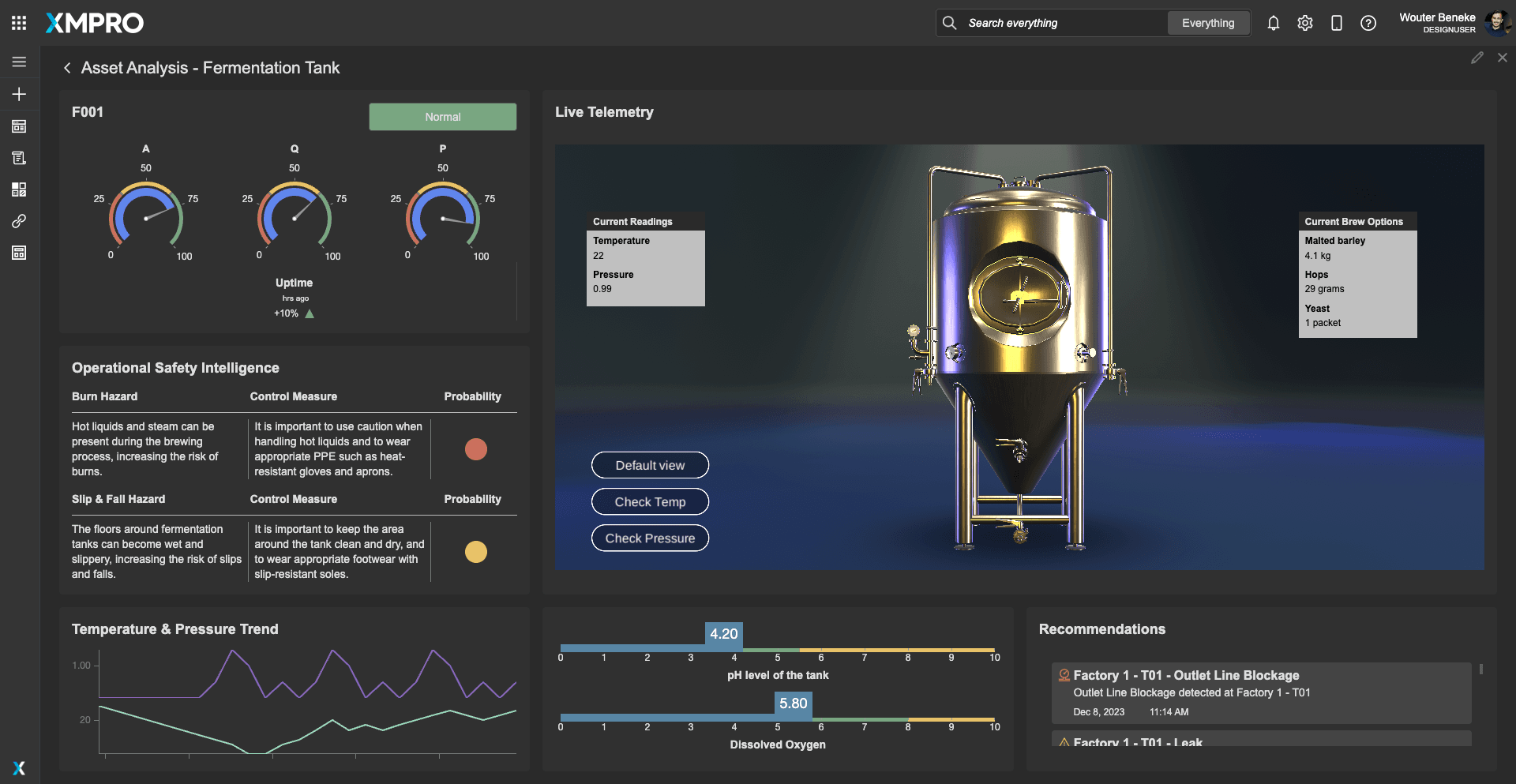
Figure 2. Real-Time Beer Fermentation Monitoring Dashboard
Overview
This Real-Time Beer Fermentation Monitoring Dashboard is an essential tool for breweries, providing a comprehensive overview of the fermentation process, a critical stage in beer production. It enables brewers to closely monitor and manage the fermentation of each batch, ensuring optimal conditions for yeast activity and beer quality.
Key Features
Integrated Fermentation Process Monitoring: The dashboard displays real-time data for each fermentation batch, including batch ID, start date/time, volume, yeast strain, and key fermentation metrics such as specific gravity, temperature, pH, and alcohol content. This integrated view allows brewers to ensure each batch progresses as planned, maintaining the desired beer profile.
Batch Progress and Fermentation Status: A visual timeline indicates the current stage of fermentation for each batch, complemented by a graphical representation of tank capacity utilization. This helps in efficiently managing tank space and scheduling subsequent batches.
Real-Time Quality Metrics and Predictive Insights: Brewers can compare current fermentation metrics against target ranges through an intuitive display, identifying any deviations in real-time. Predictive analytics powered by XMPro Co-Pilot offer foresight into the batch’s final quality, with recommendations for adjustments to maintain the desired beer characteristics.
Historical Performance and Trend Analysis: The dashboard provides a historical overview of fermentation performance, highlighting trends and deviations from target conditions. Predictive trend lines for critical parameters like temperature and specific gravity help anticipate adjustments needed to ensure consistent beer quality across batches.
Actionable Recommendations for Process Optimization: XMPro generates specific recommendations to address identified issues, such as adjusting fermentation temperature or oxygen levels to correct deviations. These targeted actions help brewers maintain control over the fermentation process, ensuring each batch meets quality standards.
Brewer Dashboard Customization: Brewers can customize the dashboard to highlight the most relevant information for their operations, including setting up alerts for critical thresholds and integrating with brewing schedules for seamless production planning.
Comprehensive Fermentation Overview: A summary section at the bottom of the dashboard provides a quick snapshot of the overall health and status of fermentation operations, including active, completed, and upcoming batches, facilitating strategic decision-making and operational planning.
Benefits
The Real-Time Beer Fermentation Monitoring Dashboard empowers breweries to optimize their fermentation process, enhancing beer quality and production efficiency. By providing detailed insights into each batch’s fermentation conditions, predictive analytics for quality control, and actionable recommendations for adjustments, breweries can achieve consistent results, reduce waste, and adapt to changing market demands. This dashboard is a cornerstone for breweries aiming to excel in beer production, combining traditional brewing art with modern technology to craft beers that consistently delight consumers.
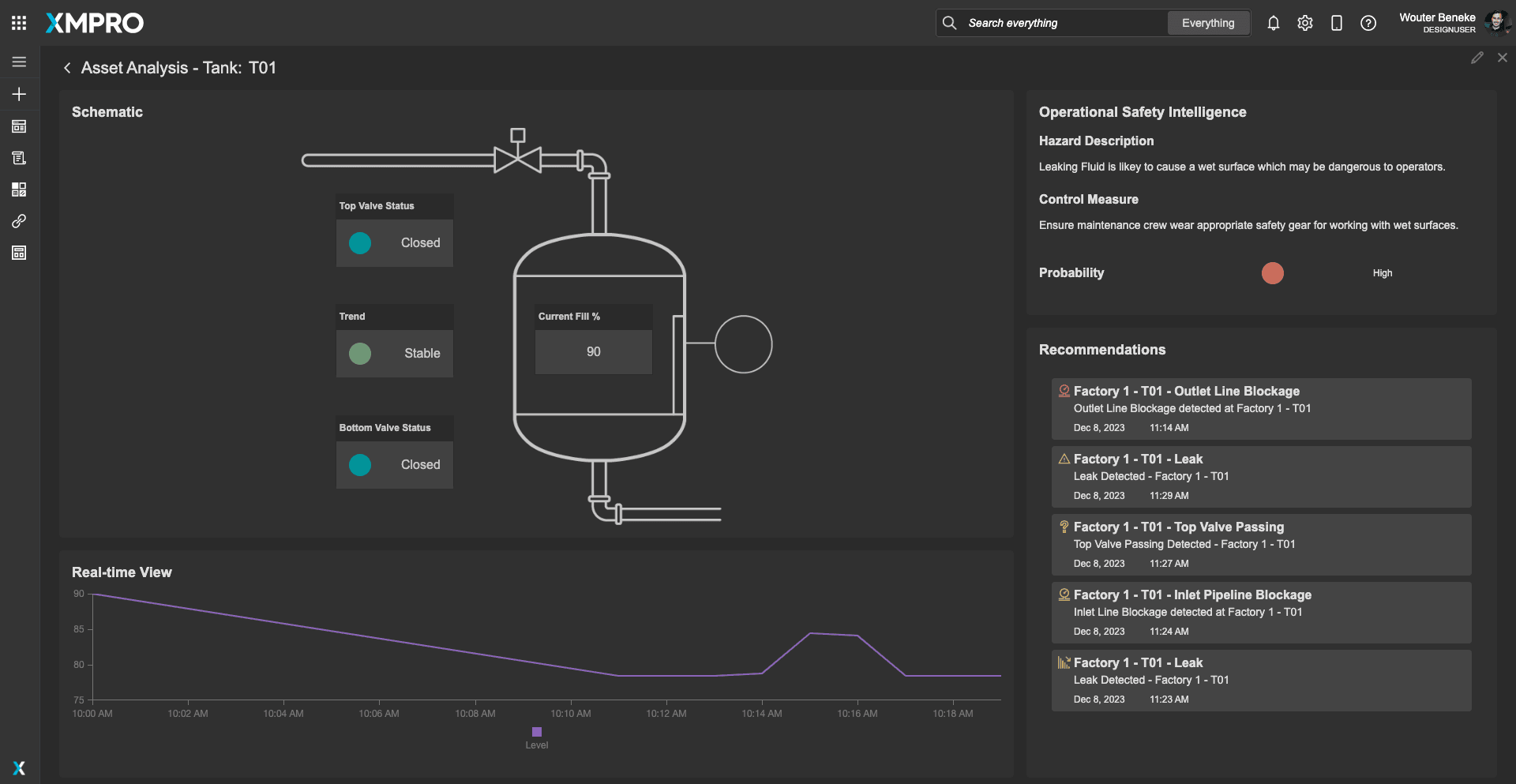
Figure 3. Advanced Conditioning and Filtration Process Dashboard for Beer Processing
This dashboard is an advanced analytical tool designed for the specific needs of beer processing, focusing on the conditioning and filtration stages. It is tailored for brewery operations, providing critical insights to ensure the final product meets the desired quality standards.
Real-Time Tank Monitoring:
The dashboard features a detailed schematic of the conditioning and filtration tank, labeled T01, showcasing real-time data on top and bottom valve statuses and the tank’s fill percentage. This immediate visual feedback allows for precise control over the beer conditioning process, ensuring optimal preparation for filtration and final packaging.
- Top Valve Status: Closed
- Bottom Valve Status: Closed
- Current Fill %: 90
Trend Analysis for Stability:
A ‘Trend’ indicator, marked as ‘Stable’, suggests consistent process conditions, crucial for maintaining beer quality through these stages. The stability of the process is key to achieving the desired clarity and flavor profile of the beer.
Operational Safety Intelligence:
The dashboard emphasizes operational safety with a dedicated section on potential hazards, such as fluid leaks, which could pose risks to brewery staff. It suggests preventive measures like wearing appropriate safety gear, highlighting the high probability of such incidents and the importance of maintaining a safe working environment.
Real-Time Process Data:
Below the tank schematic, a real-time view graph plots critical parameters over time, such as the level of liquid in the tank, providing insights into the process dynamics. This data is essential for monitoring the effectiveness of the conditioning and filtration stages and making necessary adjustments.
Recommendations for Process Optimization:
A list of time-stamped recommendations addresses immediate concerns within the tank environment, such as blockages or leaks, which are critical for maintaining uninterrupted and safe beer processing. These actionable insights are designed to prevent operational delays and ensure the integrity of the beer conditioning and filtration process.
- Recommendations include the following:
- Outlet Line Blockage
- Leak Detection
- Valve Performance Issues
Enhanced Operational Response:
The layout of the dashboard is designed to facilitate quick understanding and response to the current conditions and potential issues with Tank T01. By enabling facility operators to monitor the tank’s status and respond to recommendations effectively, it ensures the conditioning and filtration process is optimized for quality and safety.
This Advanced Conditioning and Filtration Process Dashboard is a vital component in the beer production line, offering breweries the tools needed to monitor, analyze, and optimize these critical stages. By integrating real-time data, safety intelligence, and actionable recommendations, it supports the production of high-quality beer, ensuring each batch meets the brewery’s stringent standards.
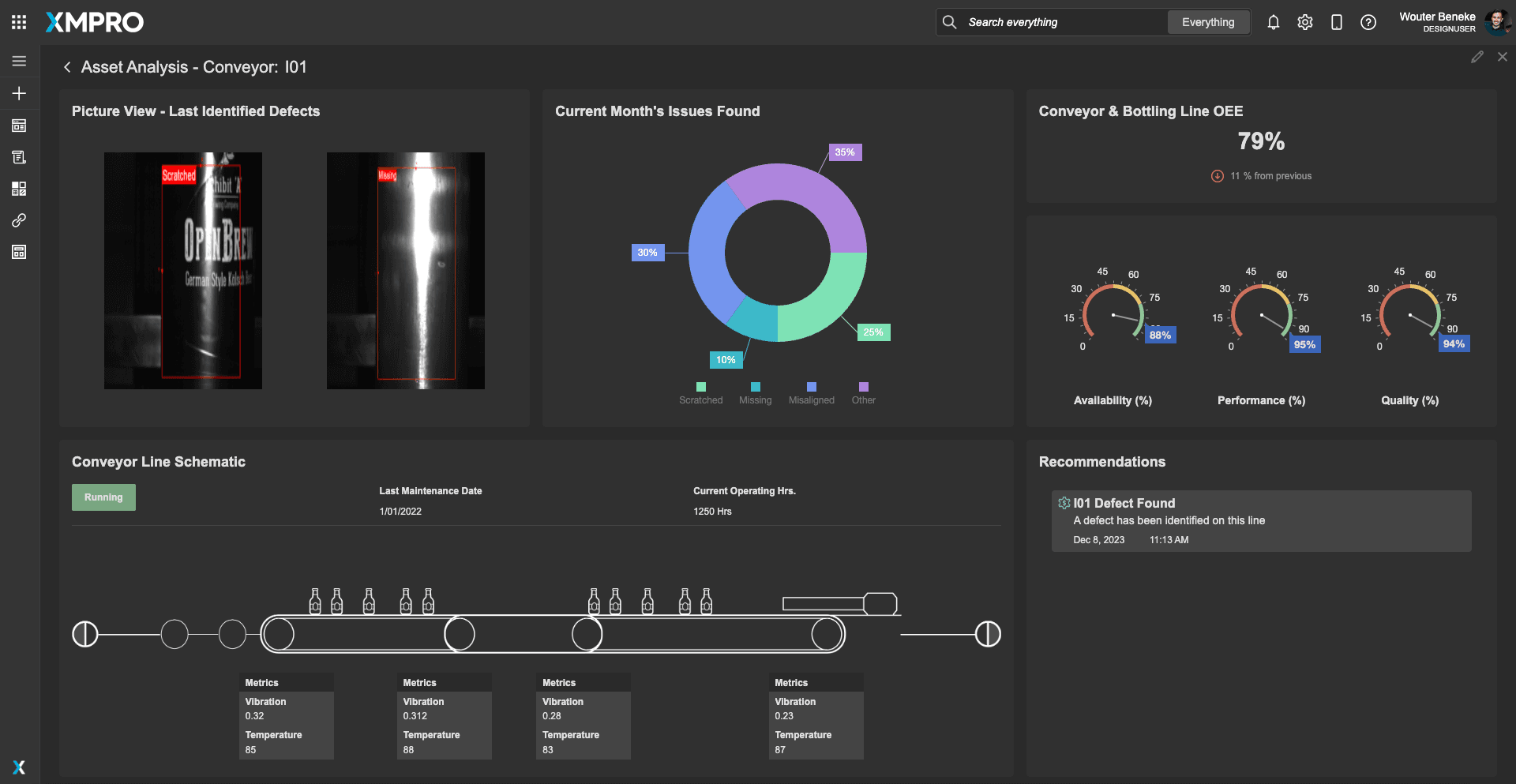
Figure 4. Advanced Conveyor and Bottling Line Monitoring Dashboard for Beer Processing
Why XMPro iDTS for Beer Processing Plant Operations?
XMPro’s Intelligent Digital Twin Suite (iDTS) is engineered to meet the intricate demands of beer processing plant operations, providing a suite of solutions that enhance efficiency, quality, and scalability across the brewing industry. Here’s how XMPro iDTS transforms beer processing through innovative technology and analytics:
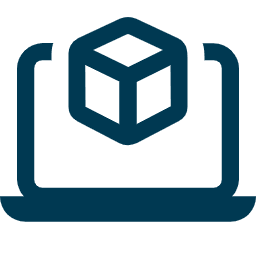
Advanced Intelligent Digital Twin Modeling:
XMPro iDTS develops sophisticated digital twins of beer processing plants, creating virtual replicas that mirror the complex dynamics of brewing operations. This technology allows for detailed performance analysis and simulation of brewing equipment and processes, such as fermentation, conditioning, and filtration, under varied conditions. It’s crucial for fine-tuning operations to achieve consistent beer quality and optimize production across different environments.
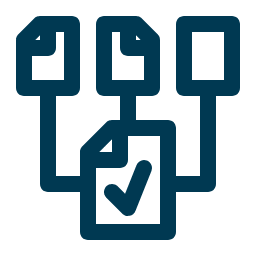
Advanced Sensor Data Integration & Transformation:
By integrating real-time data from sensors installed on brewing equipment, XMPro iDTS captures essential metrics like temperature, pressure, and flow rates. This comprehensive monitoring facilitates the detection of operational inefficiencies and quality variances, enabling breweries to maintain high standards of production and efficiency across the brewing process.
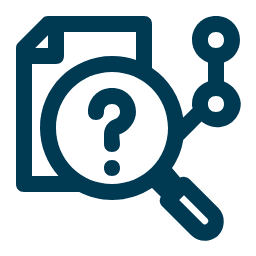
Predictive Analytics for Performance Enhancement:
Utilizing state-of-the-art predictive analytics, XMPro iDTS predicts potential disruptions and identifies optimal operational settings for brewing equipment. This predictive capability allows breweries to make proactive adjustments, enhancing the quality of the beer, maximizing yield, and reducing waste and downtime.
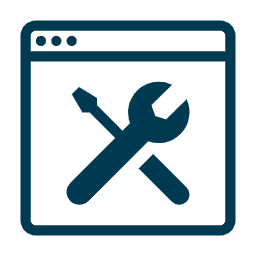
Maintenance Scheduling Optimization:
XMPro iDTS leverages equipment performance data to refine maintenance schedules, shifting from reactive to predictive maintenance strategies. This optimization ensures timely maintenance actions across multiple facilities, improving equipment reliability and minimizing production interruptions.
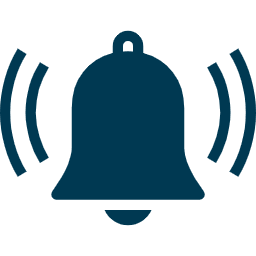
Real-Time Monitoring and Predictive Alerting:
The platform generates automated alerts and recommendations for equipment adjustments based on real-time data analysis and predictive insights. This feature minimizes manual intervention, ensuring that brewing operations are consistently running at peak efficiency.
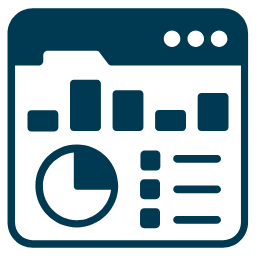
Customizable and Interactive Dashboards:
Offering real-time visibility into the operations of beer processing plants, XMPro iDTS’s customizable dashboards allow for an interactive exploration of operational data. Managers can drill down into specific process details, facilitating informed decision-making and centralized control over brewing operations.
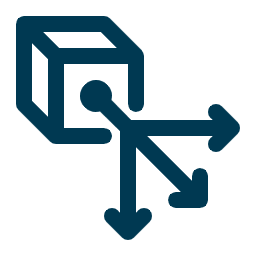
Scalability and Flexibility – Start Small, Scale Fast:
XMPro iDTS’s scalable and flexible architecture is designed to grow with your brewery, supporting operations of any size. Its modular design ensures easy integration with existing systems, allowing breweries to adapt to evolving market demands and production needs efficiently.
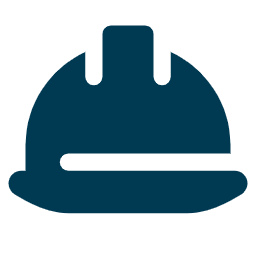
Enhanced Safety & Operational Efficiency:
By identifying potential operational hazards and inefficiencies, XMPro iDTS enhances safety and operational efficiency within the brewery. This proactive approach ensures a safer working environment and streamlined production processes..
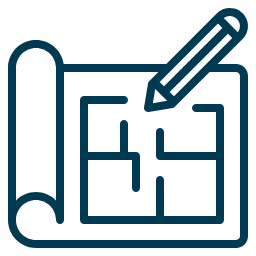
XMPro Blueprints – Quick Time to Value:
With XMPro Blueprints, breweries can rapidly deploy digital twin solutions, leveraging pre-configured templates based on industry best practices. This accelerates the digital transformation journey, enabling quick realization of operational efficiencies and quality improvements.
XMPro iDTS stands out by providing beer processing plants with a comprehensive, predictive, and integrated solution for managing complex brewing operations. Its digital twin technology, combined with deep analytics and user-friendly dashboards, empowers breweries to achieve exceptional operational efficiency, product quality, and innovation.
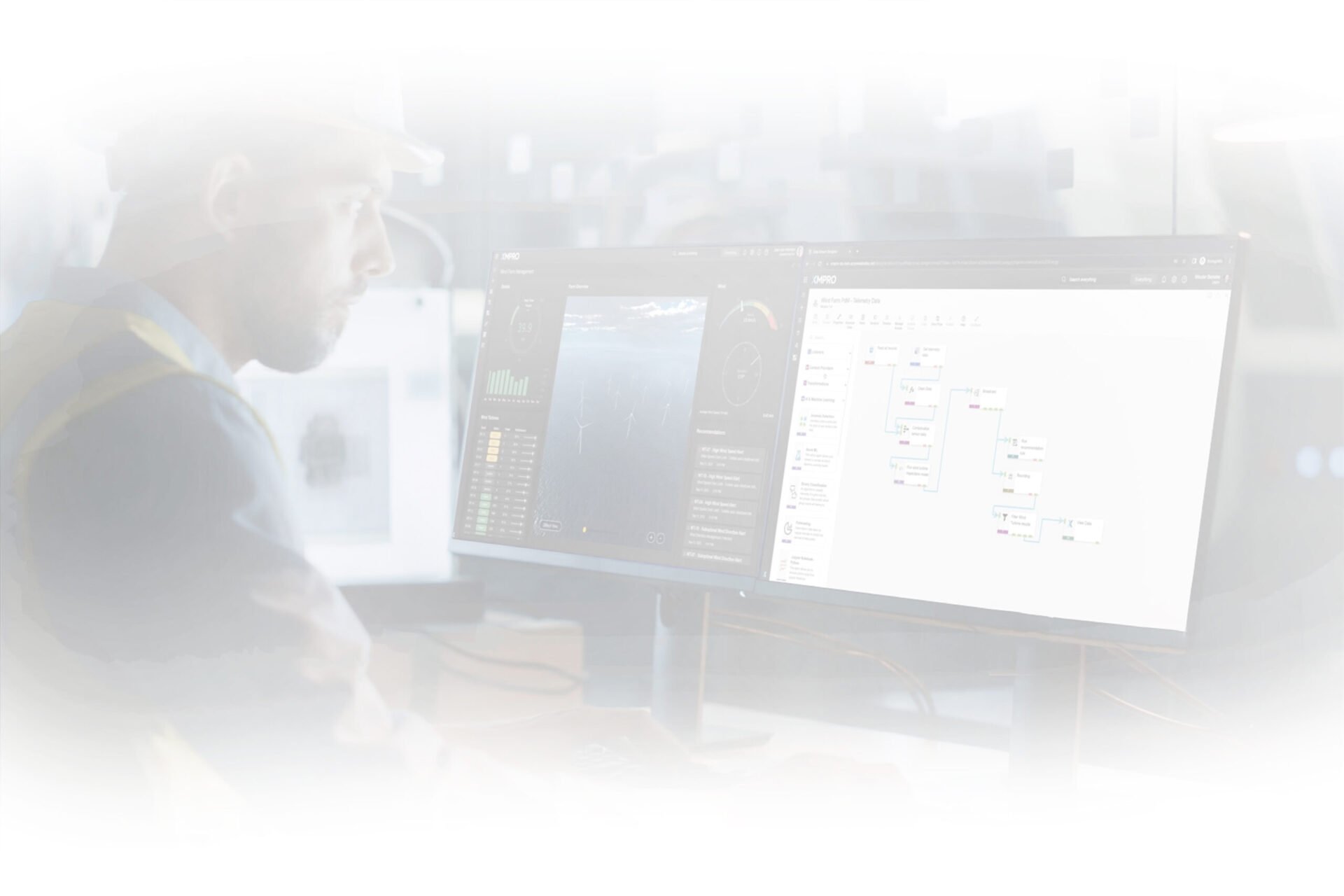
Not Sure How To Get Started?
No matter where you are on your digital transformation journey, the expert team at XMPro can help guide you every step of the way - We have helped clients successfully implement and deploy projects with Over 10x ROI in only a matter of weeks!
Request a free online consultation for your business problem.
"*" indicates required fields